Downloads
Download


This work is licensed under a Creative Commons Attribution 4.0 International License.
Review
The Development Status of Composite Materials and Winding Process of Type IV Hydrogen Storage Cylinder
Jinying Wu 1, Rui Wang 1, Ruisheng Liu 2, and Zhuo Zhang 1,*
1 College of Mechanical and Vehicle Engineering, Linyi University, Linyi 276000, China
2 Linyi Power Supply Company of State Grid, Linyi 276005, China
* Correspondence: zhangzhuoqust@163.com
Received: 27 September 2024; Revised: 2 March 2025; Accepted: 6 March 2025; Published: 19 March 2025
Abstract: In the context of the energy crisis, hydrogen energy has become a key research object in various countries due to its advantages. This article introduces the selection and molding process of Type IV hydrogen storage bottle liner materials, intermediate and surface fiber materials, winding methods and process selection, and constructs the components of the entire production process, describing the current development status of hydrogen storage bottles. By elaborating on the preparation process and materials used for Type IV hydrogen storage bottles, it is pointed out that current materials and safety have significant limitations on the development of hydrogen storage bottles, and the direction of lightweight and low-cost development is clarified. We hope that this article can help China’s Type IV hydrogen storage bottles achieve complete independence as soon as possible.
Keywords:
hydrogen cylinder filament winding carbon fiber epoxy resin1. Introduction
Since entering the 21st century, countries have begun to seek alternative energy sources such as oil and other fuels. In many renewable energy sources, hydrogen energy has caused the development of countries with the advantages of absolute clean, high energy, and can be prepared in large quantities, and is considered to be the perfect substitute for oil. The international situation is turbulent, and the increase in the cost of oil has strengthened the determination of all countries, especially China, to develop new energy. The “14th Five-Year Plan for National Economic and Social Development of the People’s Republic of China and the Outline of China’s Long-Range Objectives for 2035” are contributing to the achievement of carbon peak and carbon neutrality goals, making a significant contribution to filling in the gaps in the hydrogen energy industry chain, advancing the revolution in energy production and consumption, and promoting high-quality development in the hydrogen energy industry. This will help break free from energy constraints, enabling a complete industrial chain for hydrogen energy [1]. In recent years, the popularity of new energy vehicles has caused a lot of impact on traditional fuel vehicles, and its stable position has been threatened by an unprecedented threat. According to the annual vehicle sales in 2023 released by the China Association of Automobile Manufacturers, new energy vehicles account for 36.1%, and it is predicted that the proportion of new energy vehicles will still increase in 2024 [2]. Unlike liquid, hydrogen has great problems in transportation, such as the need for special transport vehicles, transportation costs, and the high cost of hydrogen storage stations [3]. Efficient and low-cost hydrogen storage and transportation technology is a necessary guarantee for achieving large-scale hydrogen use in the development of the hydrogen energy industry. At present, the typical storage and transportation methods of hydrogen mainly include high-pressure gaseous storage and transportation [4], low-temperature liquid storage and transportation [5], organic liquid storage and transportation [6], and solid-state storage and transportation technologies [7]. Gaseous storage and transportation are currently the mainstream storage and transportation methods for hydrogen, with mature technology and low cost, including storage and transportation. That is, the onboard hydrogen storage tank. Gaseous hydrogen storage uses high-pressure gas cylinders as hydrogen storage containers, which store gaseous hydrogen through high-pressure compression. Its main advantages are that the structure of the hydrogen storage container is simple and the filling and discharging speed is fast. At present, it has developed into a fully composite lightweight fiber winding type IV bottle, but it is not yet perfect [8]. Low-temperature liquid storage and transportation have the advantages of high hydrogen storage density and high energy density, and have huge development space and potential. Low-temperature liquid storage and transportation first liquefies hydrogen gas at a temperature of -250 ℃ and then stores it in a low-temperature adiabatic vacuum container. Hydrogen liquefaction is time-consuming and energy-consuming; therefore, low-temperature liquid hydrogen storage is commonly used for medium to large-scale hydrogen storage and applications. Qiu Yinan et al. [9] found that stainless steel is the most widely used low-temperature material for liquid hydrogen storage and transportation containers. However, different grades of stainless steel also have different applications, which usually require comprehensive consideration of their low-temperature performance, corrosion resistance, and welding performance. At present, low-temperature liquid hydrogen storage has a great market space, but there is still a certain gap before it can be applied in the market. It is urgent to solve the problems of low temperature and storage of hydrogen gas. The principle of organic liquid storage and transportation is to utilize the reversible reaction between certain unsaturated liquid organic compounds such as olefins, alkynes, or aromatic hydrocarbons and hydrogen gas and to achieve hydrogen storage through hydrogenation reaction. It can be transported at room temperature and pressure, which is convenient and safe. Solid-state hydrogen storage has a high hydrogen storage capacity, does not require high pressure or insulated containers, and has no explosion hazard, making it an ideal hydrogen storage technology. Solid-state hydrogen storage is mainly divided into physical adsorption and chemical hydride storage. The former utilizes activated carbon, carbon nanotubes, carbon nanofibers, and carbon-based materials to physically adsorb hydrogen gas. The latter is the use of metal hydrides for hydrogen storage. Fan Jingming et al. [10] pointed out that solid-state hydrogen storage materials, such as activated carbon, carbon nanotubes, and carbon nanofibers, can be improved through surface modification and the addition of catalysts, resulting in excellent hydrogen storage performance, high hydrogen storage capacity, and good hydrogen storage kinetics. In metal hydrides, magnesium has the theoretically highest hydrogen storage capacity (7.6% by weight), is lightweight, and has a relatively low cost. Ismail M [11] used hafnium tetrachloride (HfCl4) as a catalyst to investigate the effect of different amounts of HfCl4 (5%, 10%, 15%, and 20%) on the hydrogen storage performance of MgH2. The results indicate that the optimal HfCl4 content to improve the hydrogen storage performance of MgH2 is 15%. Jalil et al. [12] characterized the phase identification and microstructure using XRD and scanning electron microscopy. The hydrogen adsorption performance was studied using the weight analysis method. The results indicate that a small amount of nickel at the nanoscale is a suitable catalyst for improving the kinetics of MgH2 while also reducing grinding time. The current key technology for solid-state hydrogen storage is the development of advanced hydrogen storage materials. However, due to some research still being in the laboratory stage, the investment cost is relatively high, which is not conducive to large-scale commercial promotion. Therefore, further development is needed. At the 7th China International Import Expo, Hyundai showcased exhibits related to hydrogen energy, such as hydrogen fuel cell buses, hydrogen fuel cell systems, and HTWO grid solutions. Toyota focuses on the field of commercial vehicles, showcasing three fuel cell systems that are equivalent to the “heart” of hydrogen fuel cell vehicles. Freya brought exhibits related to hydrogen energy, including 400 L 70 MPa IV-type hydrogen storage bottles, heavy-duty truck hydrogen storage systems, and large-volume hydrogen storage and transportation solutions. Foreshadowing a development direction for future automobiles [13]. At present, China is also keeping up with the direction of technological development. CIMC Sikang Hydrogen Energy Development (Hebei) Co., Ltd. has launched the CIMC Sikang IV-type vehicle-mounted hydrogen storage cylinder and hydrogen supply system project. After completion, this project will achieve an annual production of 150,000 IV-type gas cylinders, 50,000 sets of hydrogen supply systems, and 400 composite hydrogen cylinder trailers, becoming the world’s top production base for vehicle-mounted hydrogen storage cylinders and hydrogen supply systems [14]. The storage of hydrogen also encounters certain challenges. The hydrogen storage pressure within hydrogen storage bottles is limited, necessitating the search for materials that exhibit good resistance to hydrogen embrittlement and are cost-effective. The advancement of hydrogen storage bottles is primarily constrained by materials. This article introduces the latest materials and manufacturing processes currently in use, with the hope of inspiring the development of lighter and safer hydrogen storage bottles, thereby propelling hydrogen-powered vehicles towards a peak of development.
2. Classification of Hydrogen Storage Cylinders
With the joint efforts of humanity, hydrogen storage bottles have been gradually perfected, the structure of cylinder liner was shown in Figure 1. From the initial all-metal structure Type I, to the Type II with a steel inner liner wrapped in fiber in a ring-winding pattern, to the Type III with an outer composite package and a metal inner liner, to the Type IV(a) with a plastic inner liner wrapped in fiber in a full-winding pattern, the Type IV hydrogen storage tank has become a focus of research worldwide due to its lightweight and fatigue-resistant advantages compared to the first three types, as shown in Table 1. Hydrogen storage bottles have a history of 60 years. Due to the backwardness of our country’s industry at that time, it was not able to catch up with the world’s first-class level in the industry. Foreign countries are currently in a leading position in the industry. Representative enterprises and scientific research institutions engaged in the research and development and production of composite hydrogen bottles abroad include Quantum Company of the United States, General Motors of the United States, Dynetek Company of Canada, Air Products Company of France, Japan Automotive Research Institute and Toyota Company of Japan, etc. They represent the highest level of the industry. At present, the leaders in the domestic hydrogen storage bottle industry are Sinoma Technology Co., LTD., Zhejiang University, and so on.
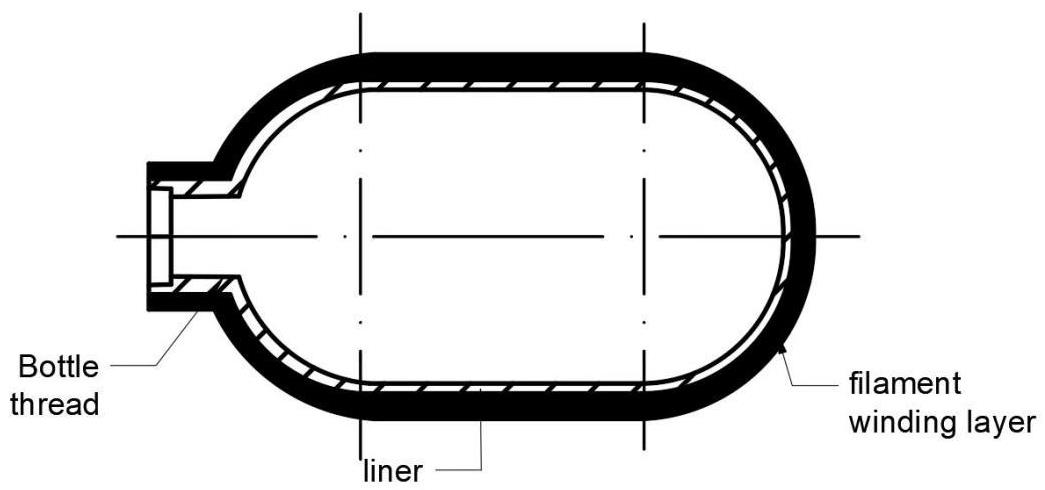
Figure 1. The structure of the cylinder liner.
Type | Type I Bottle | Type II Bottle | Type III Bottle | Type IV Bottle |
---|---|---|---|---|
Working Pressure (MPa) | 17.5–20 | 26.3–30 | 30–70 | 30–70 |
material | Chromium molybdenum steel | Steel liner fiber annular winding | Aluminum liner fiber full winding | Plastic liner fiber full winding |
Application situation | Fixed storage applications, such as hydrogen refueling stations | Fixed storage applications, such as hydrogen refueling stations | Domestic car | International car |
Product weight/volume ratio (kg/L) | 0.90~1.3 | 0.60~0.95 | 0.35~1.00 | 0.30~0.80 |
Service life (years) | 15 | 15 | 15~20 | 15~20 |
Hydrogen storage density | 14.28~17.23 | 14.28~17.23 | 40.4 | 48.8 |
3. Development Trends (Characteristics) of On-Board Hydrogen Storage Cylinders
At present, the main on-board hydrogen storage cylinders applied in the market are divided into two types: metal liner fiber-wound cylinders (Type III) and plastic fiber-wound cylinders (Type IV). Type III hydrogen storage cylinders are mostly used in China [16]. Zheng Jinyang, Li Jingyuan [17] and others have pointed out that on-board hydrogen storage cylinders have characteristics such as limited volume and weight, special requirements for filling, long service life, and variable usage environment. The manufacturing process of the Type IV hydrogen cylinder is shown in Figure 2.

Figure 2. Hydrogen Storage Cylinder Preparation Process.
3.1. Lightweight
The weight of the hydrogen storage cylinder has a great relationship with the cruising range and driving speed of hydrogen energy vehicles. The lightweight of the cylinder also reduces the cost compared to before. Compared with the metal liner fiber-wound cylinder, the Type IV hydrogen storage cylinder has a relatively small mass due to the use of composite materials for the liner, which conforms to the lightweight standards of new-era vehicles.
3.2. High-Pressure Hydrogen Storage
In the limited space of the hydrogen storage cylinder, if more hydrogen is to be stored, increasing the pressure is an essential operation. Metal liner fiber-wound gas cylinders are mostly used in China, and the working pressure is mostly 35 MPa. When storing more hydrogen, the volume and mass will inevitably increase, which is contrary to the requirements for the driving, appearance, and safety of the vehicle.
3.3. Safety
Since the Type IV hydrogen storage cylinder has a plastic liner with good toughness, it is not prone to fatigue failure and can withstand the huge pressure cycling and temperature changes during hydrogen charging and discharging. Hydrogen can easily cause hydrogen embrittlement and other problems, reducing the performance of metals and causing cracks [18]. The composite liner of the Type IV hydrogen storage cylinder can effectively prevent this situation. Therefore, the service life and safety of the Type IV hydrogen storage cylinder are much greater than that of the Type III hydrogen storage cylinder. Type III hydrogen storage cylinders need regular inspections during use to ensure safety. Type IV hydrogen storage cylinders can reduce maintenance costs.
3.4. High Storage Density
At present, metal liner fiber-wound cylinders are still mainly used in China. A 70 MPa Type III hydrogen storage cylinder has been successfully developed, and its hydrogen storage density has reached 3.9%. However, the hydrogen storage density of the Type IV hydrogen storage cylinder exceeds that of the Type III hydrogen storage cylinder by 1.6 percentage points, reaching 5.5%. The Type IV hydrogen storage cylinder adopts the structure of a plastic liner and a carbon fiber winding layer. Compared with traditional metal liner gas cylinders, it has a lighter weight and higher hydrogen storage density, which enables hydrogen energy vehicles to store more hydrogen in the same size space and greatly extends the cruising range.
4. Development of Key Technologies for Type IV Hydrogen Storage Bottles
4.1. Inner Tank Design and Manufacturing
The inner tank of the hydrogen storage bottle is an effective component to block the gas from penetrating out, and it also needs corresponding strength. In the design process of the inner liner, the inner liner is subjected to tensile stress, which is a key factor affecting its life [3]. During the process of filling and discharging the hydrogen storage bottle, fatigue cracks will occur in the inner tank, which will gradually deteriorate. And the volume of hydrogen is very small, it is easy to escape, and it will have a hydrogen embrittlement effect with metal materials, which will reduce metal plasticity [19]. Then, non-metallic materials become the first choice. The polymer liner base material of IV hydrogen storage cylinders is mainly HDPE or PA. HDPE has good stability and corrosion resistance. Compared with other materials, its cost is relatively low, and it is one of the main liner materials for Type IV hydrogen storage cylinders at present; PA6 has good strength and toughness. PA has lower hydrogen permeability than HDPE at different temperatures, as shown in Figure 3.
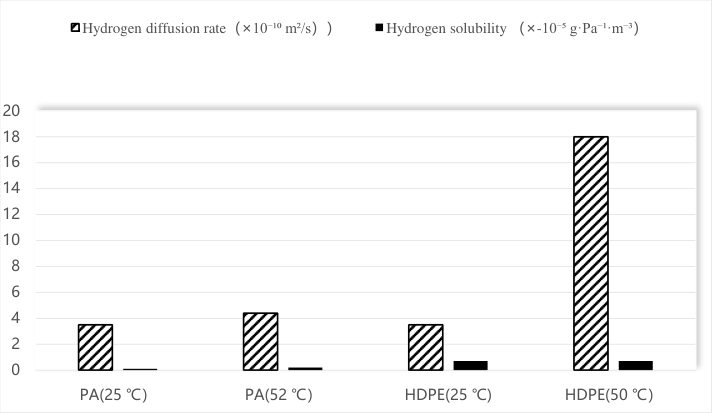
Figure 3. The comparison of hydrogen permeability between HDPE and PA.
Due to mechanical properties and gas permeability, the inner liner of type IV hydrogen storage bottle will produce two kinds of failure forms, namely, collapse caused by unstable plastic inner liner and foaming caused by yield [20]. Ito [21] measured through experiments that the diameter of PA material is 1.4 × 10-10 mol H2/(m·s·MPa). Humpenöder [22] found through experimental testing that the D of HDPE at 20 ℃ is 1.9 × 10-10 m2/s, S is 4.3 mol H2/(m3·MPa), and Φ is 8.2 × 10-10 mol H2/(m·s·MPa). Dao et al. [23] tested the hydrogen permeability of HDPE and PA and found that the hydrogen permeability of PA material was better than that of HDPE, and the anti-foaming performance of PA was better than that of HDPE. However, non-metallic materials can also penetrate; when designing the liner, the relevant penetration rate should be calculated. The permeability of the non-metallic liner is calculated based on Fick’s first law. The penetration rate of the non-metallic liner is not only related to the thickness of the liner and the pressure difference between the inside and outside, but also related to the properties of the non-metallic liner material, such as polymer type, side chain structure, density, and so on. Marshall M [24] used the mixture equation to calculate the hydrogen release rate required to obtain the steady-state hydrogen concentration to determine the formulation of the permeability index. The blow molding experts of Cotes Machinery Manufacturing Co., Ltd. [25] have successfully used the extrusion and blowing process to produce a high-capacity nylon (PA) hydrogen pressure vessel liner. The special nylon can meet the permeability resistance requirements of a hydrogen tank liner due to its excellent barrier property. Pepin et al. [26] tested the hydrogen permeability coefficients of PA6 and PA12 as type IV gas cylinder liner materials. Neto et al. [27 ]produced two types of 95 wt% low linear density polyethylene and 5 wt% HDPE composite gas cylinders by rotational molding process, which were used to prepare a fully composite carbon/epoxy resin compressed natural gas shell. The water pressure blasting test was carried out on the type IV gas cylinder liner composite composed of 95 wt% linear low-density polyethylene and 5 wt% HDPE, and it was confirmed that the design and failure of the polymer liner met the Von Mises and Tsai-Wu failure criteria. Sun et al. [28] prepared PA6/layered inorganic component liner composites for type IV gas cylinders and conducted performance tests on PA6/LIC materials used in the plastic liner of type IV hydrogen storage bottles by injection molding process. The results showed that PA6/LIC liner materials exhibited better thermal, mechanical, and rheological properties than PA6. Osman et al. [29] studied that DODAC and MMT content are proportional to the mechanical properties and oxygen barrier properties of HDPE/MMT composites by preparing HDPE/MMT composites. Wang Liang [30] studied the distribution of temperature difference stress and thermo-mechanical coupling stress of each layer on the cylinder wall during the fast-charging process of the gas cylinder by constructing a finite element model and based on the ABAQUS sequential thermo-mechanical coupling analysis method. The influence of the temperature rise effect on the mechanical properties of the gas cylinder was analyzed. Compared with blow molding, injection molding, pressure molding, etc., the inner liner is rotonized, which has the advantages of no weld, impact resistance, uniform wall thickness, and economy [20]. Ren Yueqing, et al. [31] studied the impact of the roto-plastic forming method on the impact performance and structure of crosslinked polyethylene at different temperatures and found that the structure of the innermost product is the key factor affecting the impact performance of a low-temperature drop hammer. The results show that the maximum air temperature (PIAT) in the rotational mold has a great influence on the impact strength of cross-linked polyethylene at -40 °C, which provides a better method for the later research and manufacturing of the liner. Wang Xiulei, et al. adopted the swing rotational molding equipment with the mold partition in-situ temperature control technology to achieve precise control of local heating and cooling of the mold, and explored and verified its feasibility for application in large-capacity and large-length-to-diameter ratio plastic inner tanks [32].
4.2. The Selection and Winding of Fiber Reinforcement Layer
The performance of the inner tank is not enough to support it to accept the action of internal gas pressure, so it is necessary to add materials with high strength and high elastic modulus [33]. Carbon fiber has become the best choice due to its advantages, but the current carbon fiber mainly relies on imports, and the localization of carbon fiber is a necessary step to get rid of containment. High-performance fibers are the main reinforcement for fiber composite materials wrapped around gas cylinders. By designing and controlling the content, tension, winding trajectory, etc., of high-performance fibers, the performance of high-performance fibers can be fully utilized to ensure uniform and stable performance of composite reinforced pressure vessels, with small dispersion of bursting pressure [34]. Like Japan’s Toray, Mitsubishi Rayon, and Amoco in the United States, they are all leaders in the carbon fiber industry. At present, the fiber winding process is a wet forming process, and the resin is epoxy resin. Wet fiber winding is to soak the fibers in glue first, and then according to the specified computer program, the fibers are regularly wound on the liner with a certain winding method, winding times, winding direction, winding speed, winding belt width, etc., and the liner will also rotate at the same time. According to different settings, the performance of the generated middle layer and the outer layer will also be significantly different [35]. In order to meet the work requirements, Yang Gang [36] mixed Hine epoxy MHR-070 and epoxy resin TDE-85 in a certain proportion and added self-formulated low-viscosity liquid curing agent and diluent to obtain a resin system suitable for wet winding molding. With the extension of time, the viscosity also increased. Huang Yeqing et al. [37] developed a resin matrix with low viscosity, high strength, and suitable for wet winding based on TDE-85 and AFG-90 resins, mixed with aromatic amine as curing agent, and had excellent adaptability to T700 carbon fiber. Hua et al. [38] used ABAQUS software to conduct finite element analysis and simulation of 35 L HDPE inner tank hydrogen storage bottle under 70 MPa, and carried out variable simulation of fiber winding Angle and winding layer thickness, etc., and found that when the length to diameter ratio of hydrogen storage bottle was 2.8~3.0, the amount of material was less. Li Xiaochao et al. [39] mixed activated carbon nanotubes with epoxy resin and prepared a T700 carbon fiber/epoxy resin multi-scale composite NOL ring by wet winding process, and studied that activated carbon nanotubes could prevent the propagation of resin cracks. Carvalho et al. [40] developed an optimization program for the non-geodesic winding of composite pressure vessels. This program can output the optimized layup design scheme. Wang Bin et al. [41] used DSC and gel time methods to optimize the type of accelerator, developed a TDE-85/aromatic amine resin system, which was used to make unidirectional composites and 150 mm standard pressure vessels, and carried out performance tests. The results showed that it was completely cured at about 60 °C, optimized the wet winding process, and improved the winding quality. The parameters of the wet winding process generally include fiber dipping, winding tension, winding speed, linear selection, etc. Only by coordinating the parameters can the optimal solution be achieved. Zou Caiyong et al. [42] analyzed the friction tension adjusting ring, carbon fiber unwinding roller, winding roller link, and synchronous movement link that affects tension according to the principle of the wet winding molding process, the test data is shown in Table 2. On this basis, the system control strategy is studied, and the PID tension control system and the target-following synchronous motion control system are designed to ensure the high quality of the winding.
Environmental Temperature during Winding/℃ | Viscosity of Glue Solution/Pa·s | Winding Tension/N | Gap of Rubber Extruding Roller/mm | Glue Content of Yarn Tape/% | Calculated Glue Content of Container/% | Measured Glue Content/% |
---|---|---|---|---|---|---|
20 | 1.2 | 40~35 | 0.25 | 56.6 | 42.0 | 36.46 |
The winding tension is an important molding process parameter for the fiber-reinforced composite shell, which directly affects the performance of the shell. Zhang Shijie et al. [43] studied carbon fiber multifilament, composite material NOL ring, and Φ 150 mm container, and proved that the optimal tension value for winding components is 50N for uniaxial fiber winding tension. Liu Bingyu et al. [44] systematically studied the formulation of high-performance and low-viscosity resin matrices by testing the properties of castables, multifilaments and containers; discussed the molding process conditions of conical shells; and preliminarily studied the precise control method of container fiber content. The treatment technology of wet molding shell surface was explored. The obtained conical container PV/W value reached 30.6 km, and the strength conversion rate of circumferential fibers reached 78.2%. The experimental results show that the process route is feasible. Chen Dan [45] studied the characteristic buckling and post-buckling characteristics of the inner liner of hydrogen storage cylinders, calculated the specific influence of winding tension on the inner liner, and proposed calculation methods and design values of winding tension corresponding to different inner liner thicknesses. The results are shown in Table 3, providing technical guidance for the development of the winding process of plastic inner liners.
Thickness/mm | Critical Back Pressure Value/MPa | Tension/N |
---|---|---|
2.0 | 0.0329 | 1.53 |
2.5 | 0.0605 | 2.82 |
3.0 | 0.097 | 4.53 |
3.5 | 0.146 | 6.83 |
4.0 | 0.216 | 10.09 |
4.5 | 0.280 | 13.08 |
5.0 | 0.392 | 18.30 |
5.5 | 0.457 | 21.32 |
6.0 | 0.657 | 30.69 |
4.3. Surface Fibers
In the structure of the hydrogen storage bottle, the surface layer plays a role in protecting the bottle body, and it must meet the requirements of explosion-proof, stab-proof, wear-resistant, scratch resistance, and has corrosion resistance and excellent mechanical properties. To meet the safety requirements of passenger cars. The wound layer of the volumetric glass fiber wound gas cylinder is mainly damaged by wear, sharp scratches, impact, and so on. At present, the commonly used fiber is Kevlar fiber, which is used as a material for body armor, and its anti-stabbing ability is excellent, as well as glass fiber. As early as the 1970s, NASA produced fiberglass and Kevlar production ring wound gas cylinders. In the 1980s, other relevant countries approved composite gas cylinders for the commercial market, and respirators became the largest market for composite gas cylinders. In the mid-1980s, high-strength carbon fiber was produced, and the superior performance of carbon fiber made the composite cylinder with higher performance applied to the aerospace field; Hydrogen storage tanks also evolved from this process [46]. Like carbon fiber, glass fiber winding is also carried out by wet winding process, and the resins are generally polyamide, epoxy phenolic, and epoxy resins. Epoxy adhesives are the most widely used in high-strength glass fiber fabrics, and their Young’s modulus E = 2.8~5 GPa, tensile strength Sigma = 50~140 MPa, and density Sigma = 1.2~1.3 g/cm3, have very excellent properties. After a large number of comparative experiments, VNIIEF researchers found that the most effective anti-explosion winding method is: the cylindrical container should be wound in a circumferential and helical manner, and the number of winding directions should be at least 3 or more, so that the winding method can ensure better performance of the bottle. The perigee engines of Chinese scientific test satellites EPKM-17 and SPJM-14 and the apogee engine housing of DFH-2A are also made of glass fiber composite materials, which weigh only 40~210 kg, effectively reducing the total launch mass of Mars [47]. This shows that glass fiber can make the bottle body both lightweight and high performance. In addition, with the development and application of natural gas, the production quantity of various compressed gas cylinders is increasing day by day. For example, the on-board 50 L and 90 L natural gas cylinders developed in China have a working pressure of 30 MPa and a designed service life of 10 years [48]. According to the existing results of high-pressure gas cylinders, many useful results for hydrogen storage cylinders can be excavated, and they can be moved to hydrogen storage cylinders almost simultaneously.
4.4. Failure Forms and Mechanisms of Liners
Hydrogen is a gas with a relatively small density and relative molecular mass in nature. Under high pressure, hydrogen will diffuse through polymer chains and occupy the existing voids or cavities in materials. When a hydrogen storage cylinder is rapidly depressurized, the hydrogen in these voids expands these cavities under the action of pressure gradient, resulting in blistering and even cracking [49]. The main factors for liner failure include depressurization speed, temperature, liner structure, maximum pressure, and liner material type [50]. Yersak et al. [51] used Henry’s law, Fick’s second law, and material yield criteria to establish a model for predicting the blistering of polymer liners in hydrogen storage cylinders during depressurization for the first time. Taking the liner thickness, yield strength, hydrogen diffusion coefficient, and depressurization rate as parameters for blistering damage, it was found that the PA liner and HDPE liner with a lower hydrogen diffusion coefficient and higher yield strength have stronger blistering resistance. The thinner the liner, the better the blistering resistance. However, an overly thin liner will seriously affect the strength of the liner. The faster the depressurization rate, the more prone to blistering. Cha Yan et al. [52] found that when the liner thickness is small, the critical collapse pressure is positively correlated with the thickness-to-diameter ratio (w/D) of the liner in a power function. Pepin et al. [26] believe that the reason for liner collapse or blistering is that the pressure difference on both sides exceeds the critical value of material strength. Melnichuk et al. [53] studied the influence of temperature on the hydrogen diffusivity and strength of materials and concluded that the higher the temperature, the greater the diffusion coefficient of materials. Hydrogen is more likely to be released from materials, reducing the possibility of blistering. Hui Hu et al. [54] determined that hydrogen leakage, bulging, fiber layer fracture, delamination, debonding, and delamination between the liner and fiber in the liner are the main reasons for the failure of composite pressure vessels, and compared and analyzed the nondestructive testing methods for defects in composite structures and their applicability.
4.5. The Valve of the Hydrogen Storage Cylinder
In recent years, the domestic new energy vehicle industry has developed rapidly. Valves are an important component of on-board hydrogen storage cylinders, and their performance is directly related to the safety and efficiency of the hydrogen storage system, playing an important role in protecting hydrogen storage cylinders [55]. High-pressure hydrogen storage cylinder valves are mainly used for controlling hydrogen intake and exhaust, regulating pressure, sealing, safety detection, and other functions. Cylinder valves are classified into 35 MPa and 70 MPa, according to hydrogen storage pressure. Domestically, for 35 MPa, there are brands such as GFI, OMB, Furui, and Shentong; for 70 MPa, there are only OMB and YOUNGDO [56]. At present, the majority of the bottle-mouth valves applied in China rely on imports. Especially for the 70 MPa bottle mouth valves, there are no corresponding design, inspection, and test standards yet. Gu Chunlin and others compared the structure, interface, and functions of GFI valves and OMB valves [57]. Liu Yang and others conducted the structural design of the 35 MPa combination valve [55]. Currently, rubber O-rings are mostly used for sealing in high-pressure hydrogen storage [58]. Rubber O-rings are prone to hydrogen absorption and swelling when exposed to high-pressure hydrogen for a long time [59], resulting in a large amount of high-pressure hydrogen leakage. If this hydrogen is ignited, a violent explosion will occur, posing a serious threat to life and property. Zhou Chilou et al. [60] used ABAQUS to establish a rubber ring model with hydrogen absorption and expansion and studied the influence of hydrogen absorption and expansion on the sealing characteristics of O-ring seals under high-pressure hydrogen. Su Hongyan et al. [61] carried out structural design on the nozzle sealing structure of Type IV hydrogen storage cylinders and used ANASYS for finite element analysis to study the influence law of the nozzle structure on sealing performance. Multistage valves are connected in series with each other, the pipeline is complex and prone to leakage. The more functional components integrated in the bottle mouth valve, the more complex the internal pipeline design of the valve, and the relatively higher the technical difficulty. It is necessary to have a compact layout with a small overall occupied space, avoid the crossing and overlapping of pipelines, ensure the appropriate installation space requirements and convenient operation of the parts, and also fully consider the realization of convenient manufacturing processes. Therefore, the integration of valves is an inevitable trend in the future. Jiao Jie and others used the AMESim simulation model to study the laws between the design parameters and design quantities of hydrogen storage cylinder combination valves and carried out lightweight design expansion of the combination valves [62]. Integration has greatly reduced the volume and weight of valves, enhancing the safety and range of hydrogen energy vehicles. Hydrogen, as the gas with the smallest relative molecular mass in nature, is highly prone to leakage during storage, posing a significant safety hazard [17]. To meet the functional requirements of the bottle mouth valve, make its structure more compact, reduce pipelines, and minimize the risk of leakage. Generally, devices such as filters, manual stop valves, solenoid valves, flow-limiting valves, temperature sensors, TPRD (thermal pressure relief device), and vent valves are integrated and installed at the bottle mouth of the hydrogen storage cylinder, which is called the bottle mouth combination valve.
Sealing materials need to have good hydrogen resistance, high and low temperature resistance, and anti-aging properties. However, when traditional rubber is used as a sealing material, it will expand when exposed to high-pressure hydrogen for a long time. To address this challenge, Zhou Chilou et al. proposed a rubber hyperelastic constitutive model coupled with hydrogen-induced strain; then, using the finite element analysis software ABAQUS, a finite element model of rubber O-ring sealing considering the hydrogen absorption expansion effect was established, and the model was verified at the same time [60]. With the continuous expansion of hydrogen energy applications, the performance and safety requirements for hydrogen storage cylinder valves will also become increasingly higher. In the future, hydrogen storage cylinder valves will develop towards higher sealing performance, better material properties, and more intelligent supervision and protection systems. Through continuous research, certain progress has been made in the aspects of material selection, structural design, sealing performance, and safety control of hydrogen storage cylinder valves, but there is still much room for improvement and many challenges for hydrogen storage cylinder valves. Further research and innovation are needed in the future to strengthen the research and development of valves.
5. Conclusions
This paper analyzes the key preparation process of type IV hydrogen storage bottle and the commonly used composite materials, and focuses on the research status of the key processes and the winding process of the composite material. Compared with HDPE, the inner liner material PA has better stability and corrosion resistance, but the hydrogen permeability of PA is lower than that of HDPE. So, there is an urgent need for a material that combines the advantages of both. The winding process mostly adopts wet winding, but the winding effect depends on the performance of carbon fiber composite materials, so the development of hydrogen cylinders depends on the development of materials. If more perfect materials can be discovered or manufactured, then hydrogen cylinders will usher in a new wave of development. Developing IV-type hydrogen storage tanks and localizing materials is an essential way to vigorously develop hydrogen energy vehicles, reduce vehicle emissions and pollution, alleviate energy shortages, and protect air quality.
Author Contributions: J.W.: data curation, writing—original draft preparation; R.W.: visualization, investigation; R.L.: supervision; Z.Z.: writing—reviewing and editing. All authors have read and agreed to the published version of the manuscript.
Funding: This research received no external funding.
Institutional Review Board Statement: Not applicable for studies.
Informed Consent Statement: Informed consent was obtained from all subjects involved in the study.
Data Availability Statement: Not applicable.
Conflicts of Interest: The authors declare no conflict of interest.
References
- Central People’s Government of the People’s Republic of China. Medium and Long-Term Plan for the Development of Hydrogen Energy Industry (2021–2035). Statistics of China Association of Industrial Automobile. Available online: caam.org.cn (accessed on 24 March 2022).
- Cui, Z.Y. Current situation and development analysis of hydrogen storage and transportation technology. China Foreign Energy 2024, 29, 31–39. (In Chinese)
- Liu, Y.J.; Jin, Y.J. Design Points of Carbon Fiber fully Wound Hydrogen Cylinder for Vehicle Aluminum inner Liner. Press. Vessel. 2009, 26, 28–33.
- Zheng, J.; Liu, X.; Xu, P.; Liu, P.; Zhao, Y.; Yang, J. Development of high pressure gaseous hydrogen storage technologies. Int. J. Hydrogen Energy 2012, 37, 1048–1057. doi: 10.1016/j.ijhydene.2011.02.125
- Preuster, P.; Alekseev, A.; Wasserscheid, P. Hydrogen storage technologies for future energy systems. Annu. Rev. Chem. Biomol. Eng. 2017, 8, 445–471. doi: 10.1146/annurev-chembioeng-060816-101334
- Kubas, G.; Kluwer, J. Metal Dihydrogen and Ó-Bond Complexes: Structure, Theory and Reactivity; Springer Science & Business Media: New York, NY, USA, 2001. doi: 10.1007/b113929
- Kalamse, V.; Wadnerkar, N.; Chaudhari, A. Multi-functionalized naphthalene complexes for hydrogen storage. Energy 2013, 49, 469–474. doi: 10.1016/j.energy.2012.11.018
- Cao, J.W.; Qin, X.F.; Geng, G. The Development Status and Prospects of Hydrogen Storage and Transportation Technology. J. Pet. 2021, 37, 1461–1478.
- Qiu, Y.; Yang, H.; Tong, L.; Wang, L. Research progress of cryogenic materials for storage and transportation of liquid hydrogen. Metals 2021, 11, 1101. doi: 10.3390/met11071101
- Fan, J.M.; Wang, Y.C.; Zheng, Z.X. Discussion about carbon-based solid-state hydrogen storage materials. IOP Conf. Ser. Earth Environ. Sci. 2022, 1011, 012008. doi: 10.1088/1755-1315/1011/1/012008
- Ismail, M. Effect of adding different percentages of HfCl4 on the hydrogen storage properties of MgH2. Int. J. Hydrogen Energy 2021, 46, 8621–8628. doi: 10.1016/j.ijhydene.2020.12.068
- Jalil, Z.; Rahwanto, A.; Handoko, E.; Akhyar, H. Hydrogen storage properties of mechanical milled MgH2-nano Ni for solid hydrogen storage material. Mater. Sci. Eng. 2018, 432, 012034. doi: 10.1088/1757-899X/432/1/012034
- Ma, X. Entering the China International Import Expo to See the 72 Changes in Cars. China Automotive News, 11 November 2024.
- Zhang, X.C. Moving towards “Smart Manufacturing” and Transforming Towards High-End. Hebei Daily, 27 August 2024.
- Hu, Z.R.; Hu, W.J.; Huang, Q.H. Overview of performance test standards for large-capacity high-pressure hydrogen storage cylinders. China Stand. 2022, 19, 181–186.
- Yang, W.G.; Li, W.B.; Lin, S. Development and Application Progress of Carbon Fiber Wound Composite Hydrogen Storage Cylinders. Fiber Reinf. Plast. Compos. 2015, 12, 99–104.
- Zheng, J.Y.; Li, J.Y.; Huang, Q.H. Technical Development Trends of Vehicle High-Pressure Fuel Gas Cylinders and Challenges Facing China. Press. Vessel 2014, 31, 43–51.
- Wu, B. Research and Design of Hydrogen Safety for Fuel Cell Vehicles. Shanghai Auto 2013, 12, 5–8.
- Barth, R.R.; Simmons, K.L.; Marchi, C.S. Polymers for Hydrogen Infrastructure and Vehicle Fuel Systems: Applications, Properties, and Gap Analysis; Sandia National Lab.: Richland, WA, USA, 2013; pp. 1–51. doi: 10.2172/1104755
- Chen, M.; Hu, Z.; Jia, X.; Yang, Q.; Shen, A.; Xu, K. Research progress on key technologies of Type IV vehicle hydrogen storage cylinder. Press. Vessel. 2020, 37, 39–50.
- Ito, Y. Permeability of gases and vapors through highpolymer films: XII the permeation and diffusion of helium. Kobunshi Ronbunshu 1961, 18, 124–132. doi: 10.1295/koron1944.18.124
- Humpenöder, J. Gas permeation of fibre reinforced plastics. Cryogenics 1998, 38, 143–147. doi: 10.1016/S0011-2275(97)00125-2
- Quang Dao, D.; Luche, J.; Rogaume, T.; Richard, F.; Bustamante-Valencia, L.; Ruban, S. Polyamide 6 and polyurethane used as linerfor hydrogen composite cylinder: An estimation of fire behaviours. Fire Technol. 2016, 52, 397–420. doi: 10.1007/s10694-014-0423-4
- Marshall, M.R. The effect of ventilation on the accumulation and dispersal of hazardous gases. Inst. Chem. Eng. 1983, 3, 82.
- Breakthrough in blow molding production of large capacity hydrogen cylinder. Mod. Plast. 2020, 3, 31–33.
- Pepin, J.; Lainé, E.; Grandidier, J.C.; Castagnet, S.; Blanc-Vannet, P.; Papin, P.; Weber, M. Determination of key parameters responsible forpolymeric liner collapse in hyperbaric type IV hydrogen storage vessels. Int. J. Hydrogen Energy 2018, 43, 16386–16399. doi: 10.1016/j.ijhydene.2018.06.177
- Neto, E.B.; Chludzinski, M.; Roese, P.B.; Fonseca, J.S.O.; Amico, S.C.; Ferreira, C.A. Experimental and numerical analysis of a LLDPE/HDPE liner for a composite pressure vessel. Polym. Test. 2011, 30, 693–700. doi: 10.1016/j.polymertesting.2011.04.016
- Sun, Y.; Lv, H.; Zhou, W.; Zhang, C. Research on hydrogen permeability of polyamide 6 as the liner material for type IV hydrogen storage tank. Int. J. Hydrogen Energy 2020, 45, 24980–24990. doi: 10.1016/j.ijhydene.2020.06.174
- Osman, M.A.; Rupp, J.E.; Suter, U.W. Gas permeation properties of polyethylene-layered silicate nanocomposites. J. Mater. Chem. 2005, 15, 1298–1304. doi: 10.1039/b417673a
- Wang, L. Research on Strength and Life of Composite Hydrogen Storage Vessels Based on Micromechanical Analysis; Zhejiang University: Hangzhou, China, 2016.
- Ren, Y.Q.; Dong, X.; Chen, X.L. Effects of rotational molding process parameters on low temperature impact performance of crosslinked HDPE. China Plast. Ind. 2017, 45, 38–42.
- Wang, X.L.; Yang, W.M.; Xie, P.C. Rotational molding process and equipment for the inner liner of high-pressure and large-capacity Type IV hydrogen storage cylinders. Press. Vessel 2022, 39, 1–9.
- Zhang, W.; Xu, J. Advanced lightweight materials for Automobiles: A review. Mater. Des. 2022, 221, 110994. doi: 10.1016/j.matdes.2022.110994
- Takeichi, N.; Senoh, H.; Yokota, T. Hybrid hydrogen storage vessel, a novel high-pressure hydrogen storage vessel combined with hydrogen storage material. Int. J. Hydrogen Energy 2003, 28, 1121–1129. doi: 10.1016/S0360-3199(02)00216-1
- Toyota Motor Corporation. High Pressure Tank: China. CN106989265A, 27 February 2017.
- Yang, G. Study on high-performance epoxy resin matrix for winding carbon fiber. Aging Appl. Synth. Mater. 2016, 45, 33–35. (In Chinese)
- Huang, Y.Q.; Zhang, K.Z.; Wang, X.J. Study on epoxy resin matrix for wet winding of carbon fiber. Thermosetting Resins 2007, 1, 27–29.
- Hua, T.Q.; Roh, H.-S.; Ahluwalia, R.K. Performance assessment of 700-bar compressed hydrogen storage for light duty fuel cell vehicles. Int. J. Hydrogen Energy 2017, 42, 25121–25129. doi: 10.1016/j.ijhydene.2017.08.123
- Li, X.C.; Sui, G.; Li, P. Effect of activated carbon nanotubes on properties of T700CF/epoxy resin composites. Glass Fiber Reinf. Plast. Compos. Mater. 2012, 2, 30–35.
- De Carvalho, J.; Lossie, M.; Vandepitte, D.; Van Brussel, H. Optimization of filament-wound parts based on nongeodesic winding. Compos. Manuf. 1995, 6, 79–84. doi: 10.1016/0956-7143(95)99647-B
- Wang, B.; Zhang, X.; Liu, A.H. Epoxy resin system for curing and winding at 60 °C. J. Mater. Eng. 2007, 4, 15–19.
- Zou, C.Y.; Yang, T.; Ge, B. Study on wet Winding System of multi-strand Carbon Fiber. Glass Fiber Reinf. Plast. Compos. Mater. 2013, Z3, 52–54.
- Zhang, S.J.; Liu, N.; Li, H. Study on the Effect of Winding Tension on the Properties of Carbon Fiber Composite Materials. Aging Appl. Synth. Mater. 2024, 53, 1–4.
- Liu, B.Y.; Wang, X.J.; Han, J.P. Preliminary Study on Forming Technology of Conical shell of Carbon Fiber Composite. Zi Hang Mater. 2000, 22, 26–29.
- Chen, D. Structural Design and Development of Type IV Composite Pressure Vessels Wound with Carbon Fiber; Wuhan University of Technology: Wuhan, China, 2019.
- Yu, B.; Liu, Z.D.; Zhao, W.W. Development and standard analysis of Composite Gas Cylinders at home and abroad (I). Press. Vessel. 2011, 28, 47–52.
- Du, Y. Mechanics, Design, Application and Evaluation of Composite Materials and Their Structures; Harbin Institute of Technology Press: Harbin, China, 2000.
- Liu, Y.X. Design and Application of Composite Products; Chemical Industry Press: Beijing, China, 2003.
- Jaravel, J.; Castagnet, S.; Grandidier, J.C.; Benoît, G. On key parameters influencing cavitation damage upon fast decompression in a hydrogen saturated elastomer. Polym. Test. 2011, 30, 811–818. doi: 10.1016/j.polymertesting.2011.08.003
- Zhang, M.; Lv, H.; Kang, H.; Zhou, W.; Zhang, C. A literature review of failure prediction and analysis methods for composite high-pressure hydrogen storage tanks. Int. J. Hydrogen Energy 2019, 44, 25777–25799. doi: 10.1016/j.ijhydene.2019.08.001
- Yersak, T.A.; Baker, D.R.; Yanagisawa, Y.; Slavik, S.; Immel, R.; Mack-Gardner, A.; Cai, M. Predictive model for depressurization-induced blistering of type IV tank liners for hydrogen storage. Int. J. Hydrogen Energy 2017, 42, 28910–28917. doi: 10.1016/j.ijhydene.2017.10.024
- Cha, Y.; Wang, X.L.; Yang, W.M. Numerical Simulation Study on the Collapse and Peeling Mechanism of Plastic Liner of Type IV Hydrogen Storage Cylinder. In Proceedings of the 17th China CAE Engineering Analysis Technology Annual Conference, Haikou, China, 21 June 2021.
- Melnichuk, M.; Gardavaud, Q.; Thiébaud, F.; Perreux, D. Temperature effect in cavitation risk assessments of polymers for hydrogen systems. Int. J. Hydrogen Energy 2020, 45, 23020–23026. doi: 10.1016/j.ijhydene.2020.05.224
- Hui, H.; Bai, H.; Huang, S. Research status of filament wound composite pressure vessels. Press. Vessel 2021, 38, 53–63.
- Liu, Y.; Liu, H.Y. Development of Combined Valve for High-Pressure Hydrogen Storage Cylinders. Gen. Mach. 2008, 9, 93–95.
- Liu, R.H.; Wang, D.Y.; Meng, L.Y. Research and Test Methods of Combined Valve for Vehicle High-Pressure Hydrogen Cylinders. Low Temp. Spec. Gases 2022, 40, 14–18.
- Gu, C.L.; Zhao, B.D.; Zhang, B. Development Status of Valves for Vehicle-Mounted High-Pressure Hydrogen Storage Cylinders in China. China Spec. Equip. Saf. 2019, 35, 5–8.
- Fujiwara, H.; Yamabe, J.; Nishimura, S. Evaluation of the change in chemical structure of acrylonitrile butadiene rubber after high-pressure hydrogen exposure. Int. J. Hydrogen Energy 2012, 37, 8729–8733. doi: 10.1016/j.ijhydene.2012.02.084
- Zhang, F.; Zhao, P.; Niu, M.; Maddy, J. The survey of key technologies in hydrogen energy storage. Int. J. Hydrogen Energy 2016, 41, 14535–14552. doi: 10.1016/j.ijhydene.2016.05.293
- Zhou, C.L.; Chen, G.H. Characterization of O-ring rubber seals in high-pressure hydrogen environment. CIESC J. 2018, 69, 3557–3564.
- Su, H.Y.; He, C.H.; Jin, B.H. Research on the sealing technology of the nozzle of 70 MPa vehicle-mounted Type IV hydrogen storage cylinder. China Spec. Equip. Saf. 2023, 39, 9–15.
- Jiao, J.; Zhang, Y.T.; Sun, L.Q.; et al. Simulation and Topology Optimization Research of Combined Valve for Fuel Cell Hydrogen Supply. Mod. Chem. Ind. 2018, 38, 221–225.